Arburg Inc. Partners with Oryx Additive to Offer Support Removal Solutions to Customers
Arburg’s Freeformer 3D printers enable efficient production of functional parts from standard injection molding granulates
Tempe, Arizona, USA, June 15, 2021 – Oryx Additive has partnered with Arburg, Inc., to provide expedited additive manufacturing support removal and finishing solutions to Arburg’s customers. Arburg is a global leading manufacturer of plastic injection molding machines and developer of the Freeformer and the Arburg Plastic Freeforming (APF) process.
Oryx Additives SCA finishing equipment, are specifically designed for the consistent removal of solvent-based or water-soluble engineered, support materials used in Additive Manufacturing (3D Printed) parts. This enables efficient, versatile, and value-based “hands free” processing of both finely detailed as well as strong, dense, industrial based geometries. Arburg’s specialty is the additive manufacturing of functional parts from production grade injection molding raw materials which fits well with what the SCA product line can offer.
Freeformer’s features are designed to enable customers to produce functional parts based on 3D CAD data, from industrial molding granulates, without the use of a mold. The machine processes plastic granulates, commercially used in injection molding equipment, for industrial end use results in single or multi-material configurations. With the Freeformer, you can additively manufacture one-off or small-volume batches from original materials. The material database for a wide variety of amorphous and semi-crystalline thermoplastics as feed stock, is growing continuously.
“Our vision at Oryx is to achieve the full potential of additive manufacturing by building a trusting and collaborative partnership with end-use and OEM customers. We are thrilled to partner with one of the most highly acknowledged world leaders in the injection molding industry as they build and expand the Freeformer technology into the additive manufacturing space. With Freeformer, Arburg has forged a new path towards industrial 3D printing by enabling the accessibility and use of advanced materials which were not attainable in the past. The combined use of the Freeformer technology and the tried-and-true SCA product family allows for reliable printing and finishing expected of industrial end use parts,” said Keith Jeffcoat, Chief Executive Officer, Oryx Additive.
“The Freeformer is the first additive manufacturing machine developed by a plastic injection molding technology company. It answers the market demand for increased flexibility and low unit cost models, built from proven end use material granulates. The highly effective, simple, and very reliable post processing available on the Oryx products were an ideal fit for our approach to market” said Gerry Berberian, National Sales Manager for Additive, Arburg, Inc.
About Oryx Additive
ORYX Additive was founded and spun off from a 25-year-old successful engineering and design-based company (PADT). The goal was to assist additive manufacturers increase output, while improving upon quality levels. This was done by developing and implementing proven, controlled, and integrated finishing technologies and processes, tailored to their unique needs. We innovate to design, develop and refine the tools, all techniques and equipment that will further enable the future of additive manufacturing.
Our Vision… Collaborate with our customers to achieve the full potential of additive manufacturing. Our Mission… Be the trusted partner in the development of comprehensive solutions to meet the needs of our customers.
About Arburg
ARBURG is one of the world’s leading manufacturers of plastic processing machines. The product portfolio encompasses ALLROUNDER injection molding machines, the Freeformer for industrial additive manufacturing, plus robotic systems and turnkey solutions. Production takes place exclusively at the parent company in Lossburg, Germany. In the customer center, numerous ALLROUNDERs and Freeformers are available for trials and sampling of customer tools. In addition, plastic parts are produced there for the company’s own requirements.
ARBURG has its own organizations at 35 locations in 26 different countries and, together with its trading partners, is present in more than 100 countries. This creates an international sales and service network that allows the company to provide first-class customer support on the ground. Of a total of roughly 3,200 employees, around 2,650 work in Germany. About 550 further employees work in ARBURG’s organizations around the world.
Further information: www.arburg.com
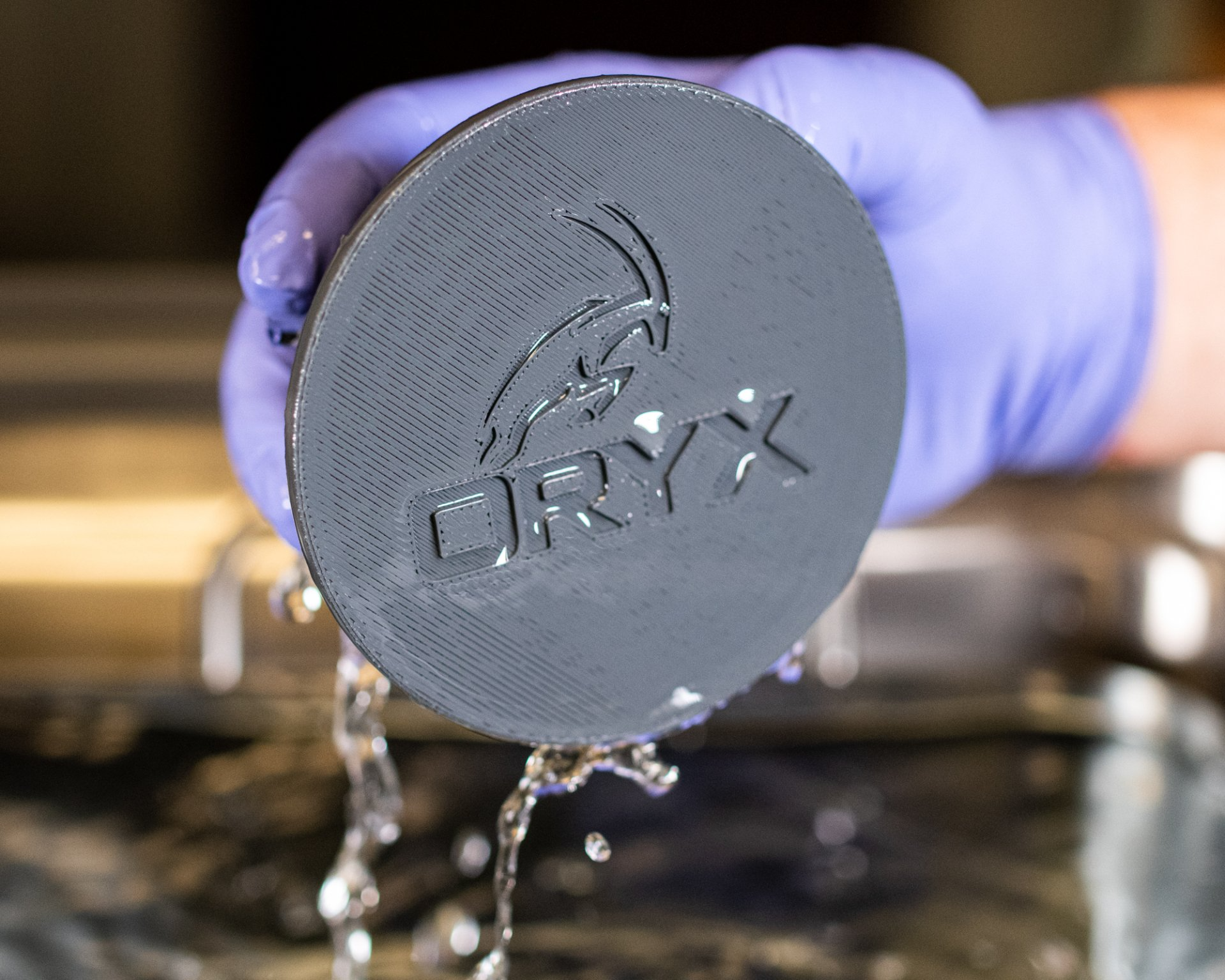
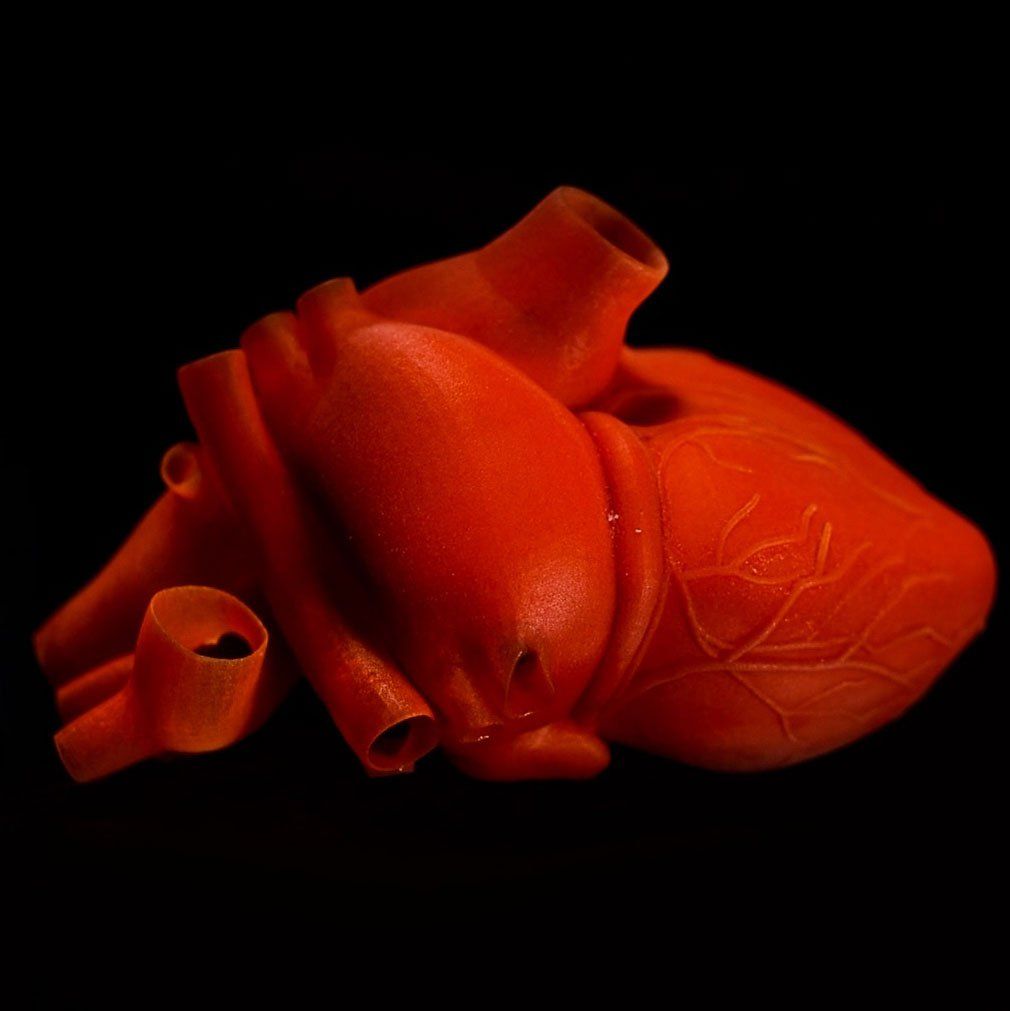